Facility Description
The Township of Neptune Sewerage Authority (TNSA) owns and operates a wastewater treatment plant located in the Township of Neptune and provides wastewater treatment for Neptune Township, Wall Township, Avon by the Sea, Bradley Beach, Neptune City, Tinton Falls, and Ocean Grove. Wastewater flow from Tinton Falls, the western portion of Neptune Township and Wall Township flow to the Authority’s force main by gravity and wastewater flow from Avon by the Sea, Bradley Beach, Neptune City, Ocean Grove and a portion of Neptune Township convey their sewage to the Authority through the Authority’s remote Laird Avenue pump station.
The plant is rated at an annual average flow of 8.5 million gallons per day (MGD) with an associated peak flow of 21.25 MGD. Treated effluent from the wastewater treatment plant is conveyed to the Atlantic Ocean by gravity via a 4 mile long 24 inch outfall pipe.
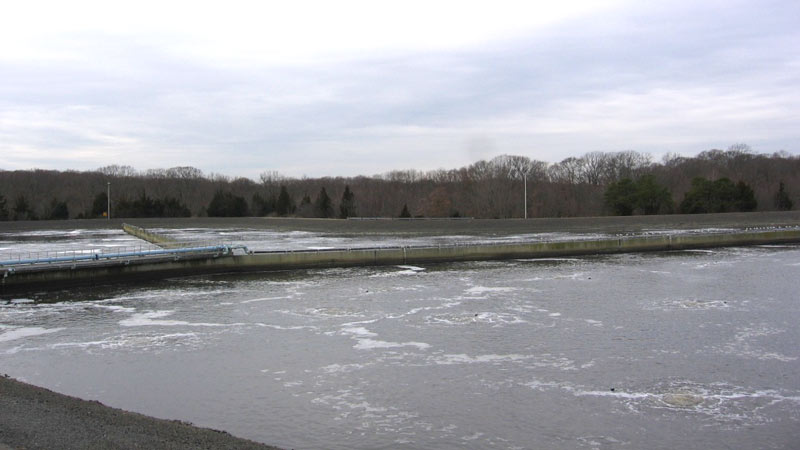
Photo 1 – Existing Stabilization Pond
The wastewater treatment plant utilizes the trickling filter fixed film process. The plant consists of three treatment trains; train numbers 1 and 2 are each designed for 2.5 MGD and train number 3 is designed for 3.5 MGD. Trains 1 and 2 receive and treat wastewater flow from the Shark River Trunk Line, Wall Trunk Line, Tinton Falls Force Main, Jumping Brook Trunk Line, Seabrook and the Atria. Train 3 receives and treats wastewater flow from the Laird Avenue Pump Station. The primary clarifiers serve as treatment units for the reduction of biochemical oxygen demand (BOD) and solids from the raw wastewater prior to entering the trickling filter tanks. The trickling filter tanks are located downstream from the primary clarifiers whose main function is for the removal of BOD and ammonia from the raw wastewater. Final clarifiers follow the trickling filters for settling of suspended solids created by the trickling filter tanks. The final clarifiers are followed by chlorination for disinfection, an aerated stabilization pond, and biological aerated filters.
The chlorinated effluent from all three treatment trains is pumped to the aerated stabilization pond, which is designed for polishing trickling filter plant effluent. The capacity of the pond is 18 million gallons, with an average depth of approximately 10 feet. The pond is equipped with fine bubble air diffusers with the air being supplied by two (2) multi‐stage centrifugal blowers each rated at 2,500 scfm at a discharge pressure of 7.0 psig. See photo 1 for stabilization pond and photo 2 for existing multi‐stage centrifugal blowers.
Existing Conditions
The existing multi‐stage centrifugal blowers have been installed and placed into operation during the mid‐1970s and have exceeded their useful life. Typically one blower is in operation 24 hours /day, 365 days/year with the second blower acting as a standby unit. The blowers operate at constant speed supplying a constant airflow volume to the aerated stabilization pond. Intake air is drawn into the blower from the inlet air filter assembly located on the roof of the Intermediate and Outfall Pump Station Building (building that the blowers are housed in) and air is discharged through a 12‐inch air main header leading to the aerated stabilization pond. The blower shown in photo 2 has experienced significant bearing and impeller failures rendering this blower inoperable thus compromising the redundancy of the aeration system.
Based upon the age of the existing blowers, the cost associated with repairing the damaged blower coupled with the desire to operate the aeration system more efficiently, TNSA has decided to replace the existing blowers with blowers that are more energy efficient in efforts to reduce aeration system electrical energy costs associated with the operation of the aerated stabilization pond and for overall system reliability. TNSA has elected to evaluate turbo blower technology as a means of providing energy efficient aeration to the existing stabilization pond.
Baseline Energy Usage
To establish the baseline energy usage for the existing multistage centrifugal blowers, instantaneous amperage readings from the operating blower control system were recorded on two separate occasions. Readings of 133 amps (discharge pressure of 6.5 psig) and 120 amps (discharge pressure of 6.0 psig) were recorded and average amperage reading of 126 amps was used to establish the baseline energy usage.
Based upon the equation P= √3 x voltage x current x power factor, the baseline energy usage is calculated to be as follows:
P = 1.732 x 480 volts x 126 amps x 0.8 power factor = 83,800 watts or approximately 84 kilowatts. The annual energy consumption was therefore calculated to be 84 kW x 24 hours/day x 365 days/year = 735,840 kW-hrs/year.
To validate the above baseline energy usage computation, a power meter was installed to monitor the blower’s actual energy consumption. The energy consumption recorded after 4,960 hours of blower operation was 89 kilowatts.
Calculated Energy Savings
Turbo Blower performance data has been provided by several blower manufacturers along with performance curves providing anticipated wire‐to‐air power at a blower discharge pressure of 6.5 psig. Upon reviewing the performance data provided by the blower manufacturers, an estimated wire‐to‐air power of 69.9 kilowatts was deemed to be reasonable and was therefore used to compute the blower’s expected energy consumption and energy savings. The projected annual energy consumption and energy savings was calculated as follows:
Energy Consumption – 69.9 kW x 24 hours/day x 365 days/year = 612,324 kW-hrs/year
The projected annual energy savings was calculated to be 735,840 kW‐hrs/year – 612,324 kW‐hrs/year = 123,516 kW–hrs/year and at an electric energy rate of 0.108/kW‐hr, the projected electrical energy cost savings was calculated to be $13,340.00.
New Jersey Clean Energy Program – Custom Measures Program
The New Jersey Clean Energy Custom Measures Program allows customers to request technical assistance to qualify unique measures of their choosing in efforts to receive energy incentives to help offset project costs. To be eligible to receive energy incentives through the Custom Measures Program, a minimum annual energy savings of 75,000 kilowatt‐hours for electric energy and 1,500 therms for natural gas must be realized as well as demonstrating project financial performance by achieving a required Internal Rate of Return greater than or equal to 10%. Incentive value for electrical energy savings is based upon $0.16/ kilowatt‐hour saved and $1.60 per annual therm saved for natural gas projects with an incentive cap of $500,000 per utility account.
Based upon the projected electrical energy savings of 123, 516 kilowatt‐hours/year, TNSA elected to participate in the Custom Measures Program and submitted their application to the New Jersey Clean Energy Program. Based upon the submitted application, the expected energy incentive was computed to be $19,762.00 with an Internal Rate of Return of 10%.
Blower Installation
The Authority evaluated several turbo blower manufacturers prior to selecting the turbo blower that would be most suited for our project. Upon the Authority’s evaluation, which included site visits to several wastewater treatment plant facilities, the Authority has selected a turbo blower manufactured by ABS SULZER. (See photo 3). The blower was commissioned on December 10, 2013 and has demonstrated over a 120 day operational period from power recording readings, an average electrical energy consumption of approximately 46 kilowatts; significantly less than the projected energy consumption of 69.9 kilowatts.
Based upon the current energy consumption of 46 kilowatts, the blower is tracking a 48% savings in electrical energy consumption or 376,680 kilowatt‐hours per year as compared to the energy consumption of the original centrifugal blower. This equates to an annual electrical energy cost savings of approximately $41,000.
The Authority has received an energy incentive check from the New Jersey Clean Energy Program in the amount of $19,425 and with an expected annual energy cost savings of $41,000; the simple payback period for this project is less than two years.
Based upon the electrical energy performance of the turbo blower, the Authority has purchased a second blower to act as a standby blower.